Zugrundeliegende Problemstellung
Aufgrund des derzeitigen industriellen Wandels ist die deutsche Automobilindustrie besonderen Herausforderungen ausgesetzt. Zum einen ist der digitale Transformationsprozess in Ländern wie China oder den USA deutlich weiter fortgeschritten. Zum anderen führen zunehmendes Umweltbewusstsein und neue technische Möglichkeiten dazu, dass sich die Industrie in kurzer Zeit auf neue Antriebs- und Produktkonzepte und damit auf neue Produktionstechnologien einstellen muss. Dies betrifft die etablierten Lieferketten und hier insbesondere hochspezialisierte Zulieferer, welche nun vor der Herausforderung stehen, neue Produktlinien in kürzester Zeit aufzubauen und in Betrieb zu nehmen. Das steigende Umweltbewusstsein sowie sich wandelnde gesellschaftliche Aspekte führen dazu, dass System- und Produktionskonzepte in der Automobilindustrie zukünftig noch stärker hinterfragt werden. Wirtschaftliche Krisen sorgen zudem dafür, dass neue und finanzstarke Anbieter auf den Markt treten, die den hochdynamischen Wandel von Technologien und Produkten beschleunigen und damit auch etablierte Unternehmen unter Druck setzen. Um diesen Druck standzuhalten, müssen insbesondere deutsche Unternehmen ihre Anpassungsmöglichkeiten erweitern und resiliente Produktionstechnologien etablieren.
Neue Technologien und Werkstoffe, zunehmende Bauteilkomplexitäten sowie ein steigendes Qualitätsbewusstsein der Abnehmer entlang der Wertschöpfungskette führen zu gesonderten Anforderungen in der industriellen Fertigungstechnik der Automobilindustrie. Die bauteilspezifische Qualitätssicherung erfolgt insbesondere bei hohen Stückzahlen in aller Regel stichprobenartig, was bei der Fertigung von kundenspezifischen Produkten nur schwer umzusetzen ist. Der Ermittlung etwaiger Fehlerursachen und deren Gegenwirkung wird aufgrund der hohen Fertigungskomplexität oftmals heuristisch und/oder mit einem enormen personengebundenen Erfahrungswissen begegnet. Zur Minimierung dieser Komplexität erfolgt diese Beurteilung in aller Regel innerhalb einzelner Bearbeitungsstufen. Die damit einhergehenden eng angesetzten Toleranzen führen zu einem hohen Anpassungsaufwand zu einem unwirtschaftlichen Betrieb der Gesamtproduktion. Dies erschwert gleichermaßen die Anpassung der bestehenden Prozesslinien auf neue Anforderungen oder Vorgaben, bspw. den Einsatz neuer Materialien oder Anpassungen von Bauteilgeometrien.
Zudem wird eine ganzheitliche Betrachtung komplexer Bearbeitungsprozesse über die Unternehmensgrenzen hinweg dadurch erschwert, dass in den einzelnen Unternehmen bisher v.a. abgeschlossene Datenerfassungs- und -verwaltungslösungen (sog. Datensilos) zum Einsatz kommen. Gründe hierfür sind u.a. unterschiedliche Entwicklungsstände bzgl. der Digitalisierung in den Unternehmen, Sorgen um Datenhoheit und Zugriffrechte, Schnittstellenproblematiken zwischen unterschiedlichen Systemen und schlichtweg die Unkenntnis über Möglichkeiten der Datenerfassung oder Bedarf der Datennutzung in benachbarten Unternehmen. Auch die mangelnde Durchgängigkeit der Bauteilidentifikation vom Rohmaterial bis zum Recycling ist hier ein wesentlicher Hinderungsgrund, da dieser Mangel bisher die Zuordnung von Prozessparametern zu individuellen Bauteilen oft unmöglich macht. Darüber hinaus stellt der Grad der Flexibilität und Selbständigkeit sowie eine noch konsequentere ad-hoc Einbindung der Mitarbeiter (und damit des Expertenwissens) in das Zentrum der digitalen Prozesse und Produktion eine anzugehende Lücke dar. Im hier skizzierten Vorhaben sollen mehrere konkrete Anwendungen unterschiedlicher Unternehmen einbezogen werden, die sich im Hinblick auf eine hohe Sicherheitsrelevanz der produzierten Bauteile, hohe Anforderungen an die Maßhaltigkeit sowie die starke, Abhängigkeit von den Materialeigenschaften ähneln. Abweichungen zu einem frühen Zeitpunkt wirken sich stark auf spätere Prozessschritte und Zielgrößen wie Qualität und Performance aus. Die wirkenden Zusammenhänge sind dabei komplex und erschweren eine adäquate Handhabung im Sinne einer funktionierenden Qualitätssicherung.
Die für dieses Projekt ausgewählten Prozessketten zeichnen sich durch eine Komplexität aus, welche exemplarisch für die meisten Fertigungsprozesse in der Automobilindustrie ist. Diese Komplexität erschwert die Handhabung von Prozess- oder Materialabweichungen erheblich und macht den Betrieb erfahrungsbasiert und kostenintensiv. Die Möglichkeit, systematisch auf die beteiligten Einzelprozesse einzuwirken und eine Einbeziehung von lieferanten-seitigen Bauteil- und Materialinformationen würde die Prozessqualität und die Robustheit der Gesamtproduktion stark erhöhen. Die Erarbeitung dieser Möglichkeiten anhand der Prozessketten der beteiligten Anwendungspartner stellt die Voraussetzungen für ein hohes Transferpotential auf andere Anwendungen.
Darstellung des Lösungsansatzes
Anhand der dargelegten Problemstellung kann festgestellt werden, dass die technischen Möglichkeiten, welche sich aus der Digitalisierung von Fertigungsanlagen ergeben, bei weitem nicht ausgeschöpft werden. So bleiben prozessrelevante Informationen noch immer in einem abgeschlossenen Teil-Ökosystem (≜ Prozessstufe), obwohl grundsätzlich die technischen Möglichkeiten existieren, diese entlang der Wertschöpfungskette weiterzugeben. Hier setzt die in dieser Skizze vorgestellte Projektidee für AdaProQ an.
Der Lösungsansatz des Vorhabens besteht darin, das Paradigma der Einzelprozess-orientierten Qualitätsgewährleistung aufzugeben, die bestehenden Betrachtungsgrenzen aufzulösen und systematisch die Gegebenheit einzubeziehen, dass sich Prozesseinflüsse bereits zu einem frühen Zeitpunkt auf spätere Zielgrößen (Qualität und Quantität der Produkte, Effizienz in der Maschinennutzung, Verbesserung der Produktivität, Bauteilperformance, etc.) auswirken können.
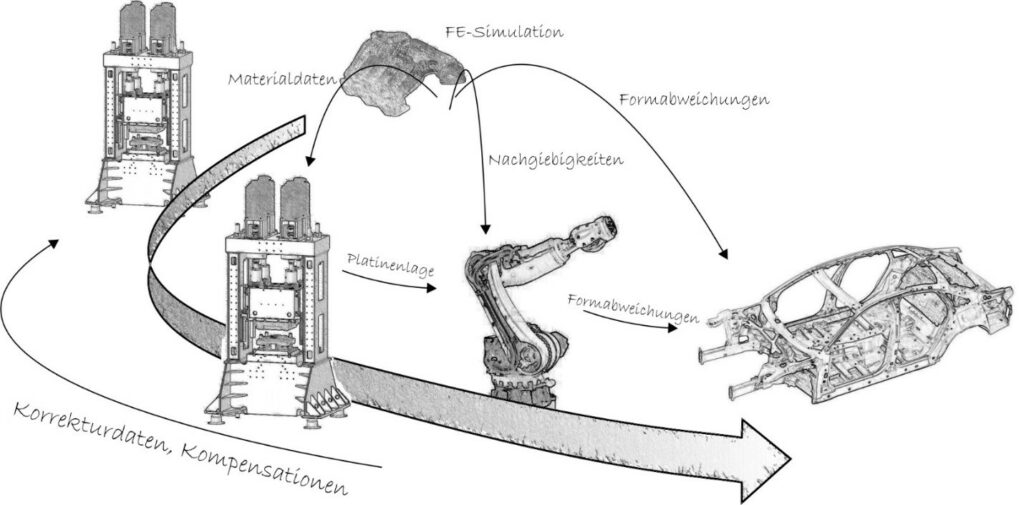
Industrieunternehmen, insbesondere OEMs und Zulieferer im Automobilbereich, sind bereits heute in der Lage, zahlreiche Prozessgrößen und Produktzustände während des Durchlaufs durch die Prozesskette erfassen zu können. Hierfür wurden bereits innerhalb der letzten Jahre umfangreiche Investitionen u.a. im Condition Monitoring getätigt. Durch das gezielte Zusammenführen dieser Daten ist es mittels geeigneter Methoden möglich, Zusammenhänge über Prozessgrenzen hinweg zu erfassen und Auswirkungen auf Zielgrößen zu quantifizieren. Ein geeignetes Datenmanagement für das Industrial Internet of Things ermöglicht dabei die effiziente Verknüpfung der einzelnen Prozessschritte mit einander sowie mit KI/Optimierungs-Applikationen
So können erkannte Abweichungen im Prozess nicht nur für die gleiche Prozessstufe genutzt werden, sondern zum einen an spätere Prozessschritte weitergegeben werden, welche somit die Möglichkeit haben, kompensierend einzuwirken (prospektiver Ansatz). Dies erlaubt es, Ausschüsse zu reduzieren oder gar zu vermeiden. Gleichzeitig eröffnet dieser Gedanke die Möglichkeit, die engen Toleranzen der Einzelprozessstufen zu überdenken.
Neben diesem vorwärts gerichteten Ansatz ist es jedoch auch möglich, diese Informationen auch für die Qualitätssicherung der nachfolgenden Bauteile zu nutzen. Konventionelle Herangehensweisen betrachten hierbei im Wesentlichen die gleiche Prozessstufe (Beispiel: Hub-zu-Hub-Regelung im Umformprozess). Die Kenntnis der wirkenden Zusammenhänge über Prozessgrenzen hinweg erlaubt es auch, intelligente Kompensationsschritte bereits in vorgelagerten Prozessschritten vorzuhalten (retrospektiver Ansatz). Sowohl die Betrachtungsgrenzen als auch die zugrundeliegenden Prozess- und Zielgrößen dieser Zusammenhänge sind dabei grundsätzlich flexibel. Damit wäre es prinzipiell möglich, zu einem relativ frühen Zeitpunkt Aussagen auf die zu erwartende Bauteilperformance zu treffen und Bauteile frühzeitig ausschleusen zu können.
Die obige Abbildung illustriert einen möglichen Anwendungsfall aus dem Bereich des Karosseriebaus (vgl. Anwendung 4 und 5). Die Übergabe von bauteilbezogenen Prozessdaten wie bspw. der Platinenlage und der damit einhergehenden Abweichung der der Maßhaltigkeit umgeformter Bauteile ermöglicht eine Kompensation dieser Abweichungen im nachgelagerten Falzprozess. Gleichzeitig lassen sich damit Qualitätsinformation der Gesamtbaugruppe ableiten, was eine frühzeitige Einordnung und Reaktion ermöglicht. Wird die abweichende Platinenlage auf systematische Ursachen zurückgeführt, ist direkt eine Anpassung der vorgelagerten Schneidoperation möglich.
Der zentrale Baustein dieser Ansätze stellt die Ermittlung, Modellierung und Anwendung der existierenden Zusammenhänge dar (vgl. Abbildung 2). Hierfür werden reale Prozessinformationen und virtuelle Sensoren aus Prozesssimulationen genutzt, um die entsprechenden Modelle (z.B. mathematische Modelle, neuronale Netze) aufzubauen. Da hierfür unterschiedliche Informationen aus verschiedenen Bereichen der Prozesskette zusammengetragen werden, sind neben der erforderlichen Infrastruktur auch geeignete Aufbereitungsmethoden erforderlich, welche bspw. eine Vorselektion oder auch vorgelagerte Reduktion übernehmen. Die Pflege bzw. die weitere Präzisierung der Modelle erfolgt ständig durch die Einbeziehung der erfassbaren Prozesszustände und den Abgleich mit gemessenen Zielgrößen. Die beschreibbaren Zusammenhänge können dann dafür genutzt werden, um optimale Vorschläge für die Prozessanpassung abzuleiten.
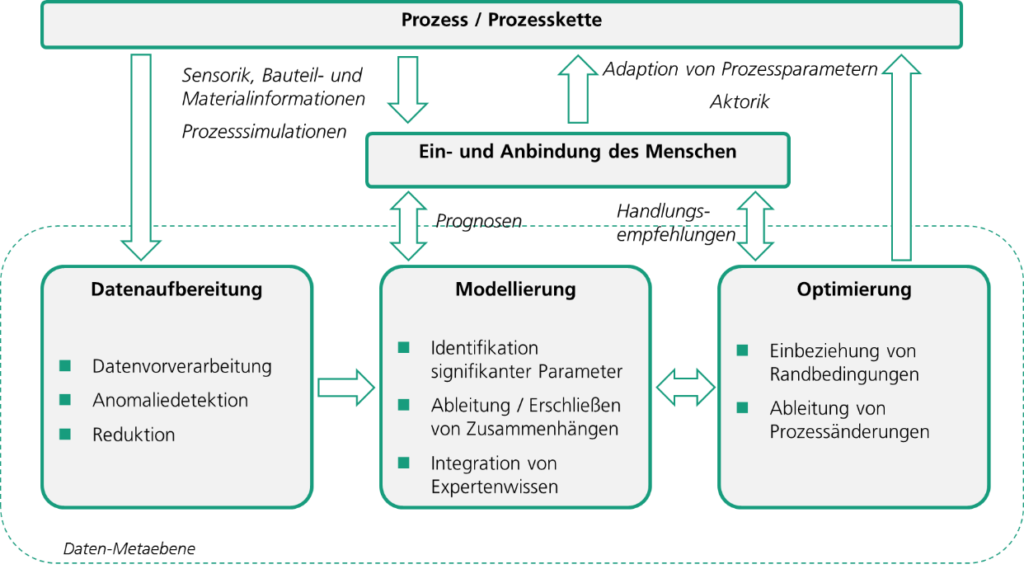
Zielstellung
Ausgehend vom zuvor beschriebenen Lösungsansatz lässt sich das Gesamtziel des Projektes wie folgt formulieren:
Entwicklung und Demonstration eines generischen Ansatzes zur Realisierung adaptiver Prozessketten in Anwendungen des Automobilbaus zur Steigerung der Produktqualität und Erhöhung der Produktionseffizienz.
Hierfür ergeben sich folgende Teilziele:
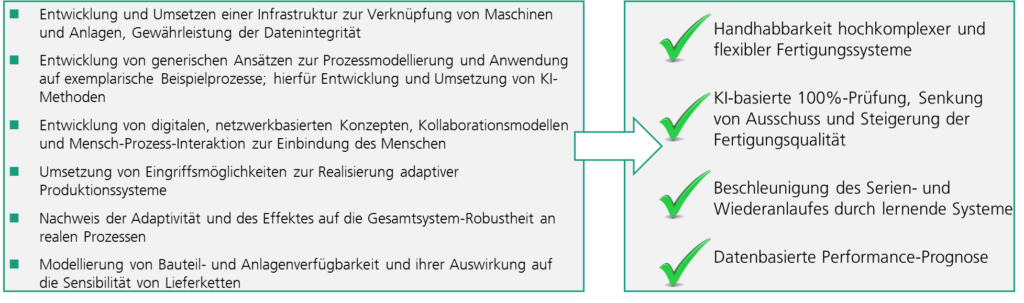
Projektorganisation
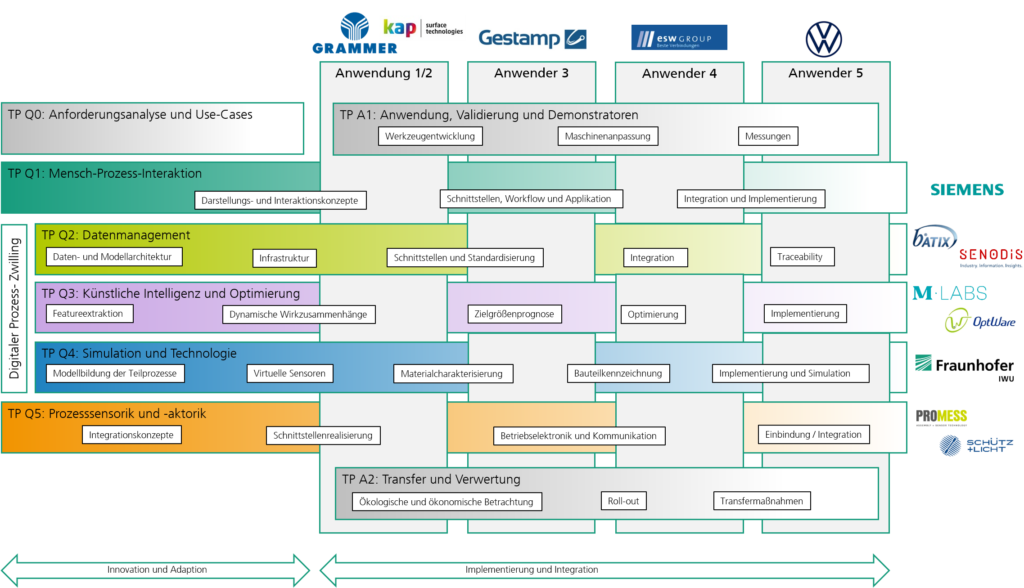